ANALYSIS OF GLASS BOTTLE/JAR PACKAGING MANUFACTURING PROCESS
Glass is a packaging material with a long history. In the case of many kinds of packaging materials pouring into the market, glass containers still occupy an important position in packaging, which is inseparable from its packaging characteristics that can not be replaced by other packaging materials.
The main raw materials of glass bottles are natural ore, quartz stone, caustic soda, limestone and so on. Glass containers have a high degree of transparency and corrosion resistance, contacting with most chemicals will not change the material properties.
Their manufacturing process is simple. What’s more, they have free and changeable shape, high hardness, heat resistance, clean, easy to clean, and have the characteristics of repeated use.
Ⅰ. Technological Process Of Production

Glass Bottle Jar Packaging Technological Process Of Production
First of all, design and manufacture mold. Second, glass raw materials plus other accessories at high temperature are dissolved into liquid, and then injected into the mold, cooling, cutting, tempering, the formation of glass bottles. Generally, glass bottles have rigid signs, and the signs are also made of mold shapes.
① Raw Material Pre-processing
The massive raw materials (quartz sand, soda ash, limestone, feldspar, etc.) are crushed, the wet raw materials are dried, and the iron-containing raw materials are treated with iron removal to ensure the quality of the glass.
② Preparation Of Compound Materials
③ Melting System
The glass compound is heated at high temperature (1550~1600 degrees) in the pool kiln or pool furnace to form a uniform, bubble-free liquid glass that meets the molding requirements.
④ Forming
The liquid glass is put into the mold to make the glass products of the required shape, such as bottles, jars, etc.
⑤ Heat treatment
Through annealing, quenching and other processes, eliminate or produce the internal stress of the glass, phase separation or crystallization, and change the structural state of the glass. All is to keep the glass container safe. This annealing process depends on the thickness of the glass and generally takes between 20 and 60 minutes.
⑥ Spraying
The bottle required by the spraying needs to enter the spraying process.
⑦ Manual Inspection
There are three kinds of inspectors: inspection of glass bottle personnel; inspection of packing personnel; sampling personnel. The samples are sent to the laboratory for glass bottle inspection. Through the laboratory tests to meet the national standards are qualified products.
Ⅱ. Important Process Analysis
1. Molding Process
The forming process of glass bottles refers to a series of combinations of actions (including mechanical, electrically controlled, etc.) that are repeated in a given programming sequence with the goal of producing a bottle with a specific desired shape.
The molding of glass bottles can be divided into three kinds according to the production method: artificial blowing, mechanical blowing and extrusion molding.
In terms of manufacturing process, it can be divided into two categories: molded bottles (using models to make bottles) and tube bottles (made with glass tubes).
At present, the production of glass bottles and jars mainly adopts the molding method, and there are two main processes: BLOW AND BLOW method for narrow mouth bottles and PRESS AND BLOW method for larger mouth bottles and jars. Less use of tube glass method.
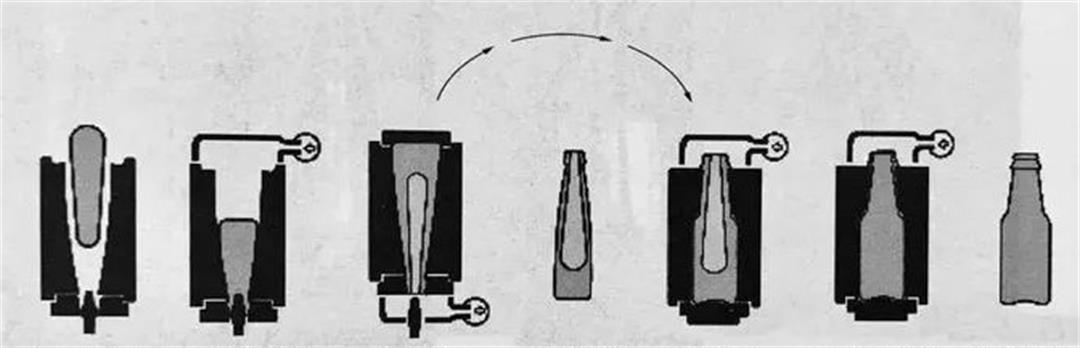
BLOW AND BLOW
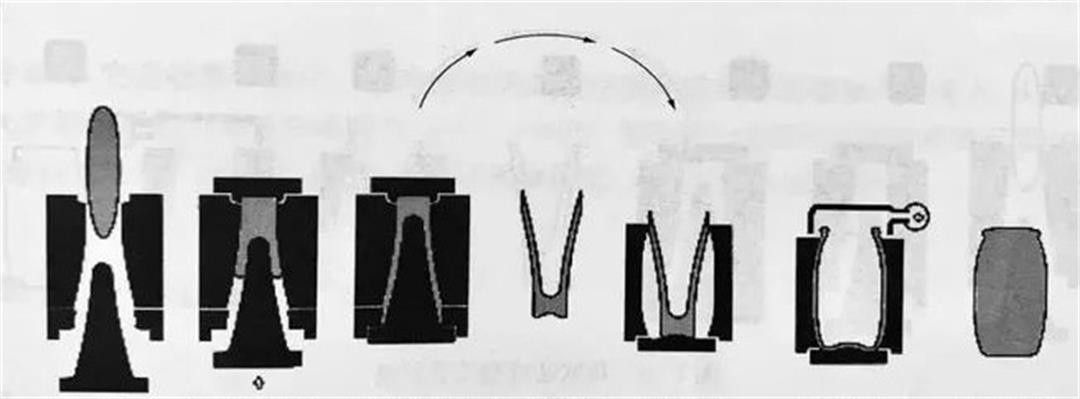
PRESS AND BLOW
Large bottle mouth, small flat mouth, threaded bottle mouth, crimp mouth and clamp mouth are all due to the difference in mold. The height of the bottle is set on the machine by our bottler. At this point, the shape and capacity of the bottle are created.
The subsequent bottles are clamped out of the mold and placed on a stop plate with bottom-up cooling air, waiting to be transported to the annealing process.
2. Bottle Making Machine
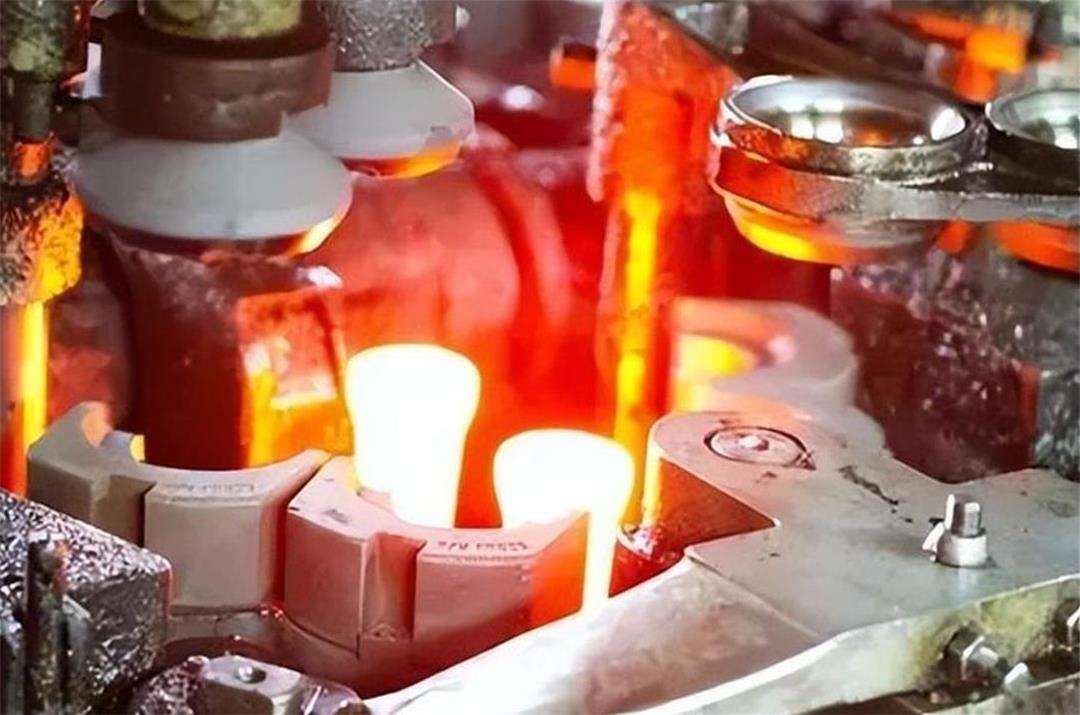
Automatic Bottle Making Machine
The production of modern glass bottles and jars is widely used in automatic bottle making machines with high-speed forming. Bottle making machine refers to the equipment that can make glass bottles and jars. In general, the bottle making machine consists of the most basic 19 actions to form a bottle. The device is opened by the electronic control of the timer system to coordinate all actions.
⑴ There are many types of automatic bottle making machines, but basically two kinds of processes: manual bottle-making machine and determinant bottle-making machine. Among them, the determinant bottle-making machine is more commonly used. Because it has a wide range and great flexibility.
⑵ Advantages of the determinant bottle-making machine process:
① The mouth mold line and the glass bottle mold line are consistent, that is, in a straight line.
② The cooling flower printing at the bottom of the glass bottle is clear.
③ The finish of the glass bottle body produced is smooth and uniform and the bottle wall is clear and transparent.
④ At the bottom of the glass bottle, the obvious dull head mark can be seen in the line process.
⑤ The bottles of the assembly line appear neat, even the angle of reflection is very consistent.
⑥ The overall production process of the glass bottle process line can adapt to the automatic production of various filling and sealing machines.
3. Spraying Process
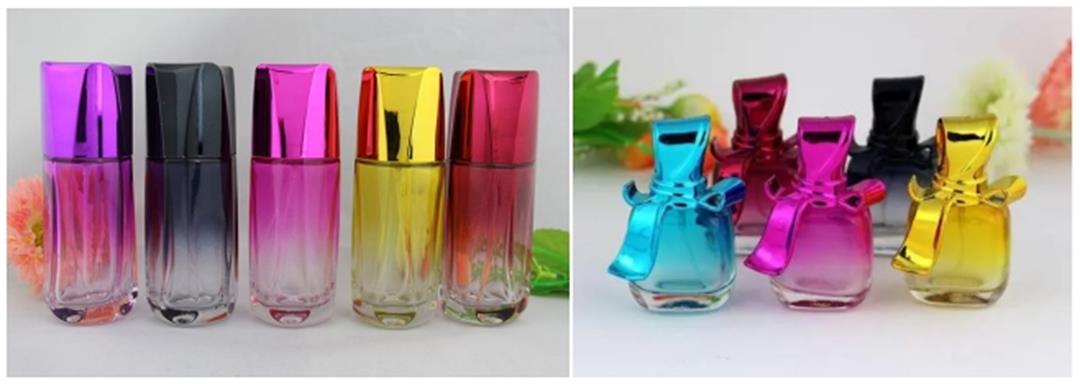
Color Spraying
The glass bottle spraying production line is generally composed of spray room, suspension chain and oven. Furthermore, the important thing is the former water treatment and need to pay special attention to the problem of sewage discharge. As for the quality of the glass bottle spraying, it is related to the water treatment, the surface cleaning of the workpiece, the electrical conductivity of the hook, the volume of the gas, the amount of powder spray, and the level of the operator.
The spraying of glass bottles is divided into pre-treatment section, preheating section, dust blowing purification section, drying section and powder spraying section.
⑴ Pre-treatment section
The pre-treatment section includes pre-stripping, main stripping, table adjustment, etc. If it is in the north, the temperature of the main stripping part can not be too low, and it needs to be insulated. Otherwise the treatment effect is not ideal.
⑵ Pre-heating Period
Generally, it takes 8 to 10 minutes. It is best to make the sprayed workpiece has a certain residual heat when arriving at the powder chamber to increase the adhesion of the powder;
⑶ Dust Blowing Purification Section
If the process requirements of the sprayed workpiece are relatively high, this section is essential. Otherwise, the surface of the workpiece after processing will have a lot of particles reducing the quality, if there is a lot of dust adsorbed on the workpiece.
⑷ Drying Section
This section should pay attention to the temperature and baking time. Generally, 180 ~ 200 degrees is better for powders, depending on the material of the workpiece. Also, the drying furnace should not be too far away from the powder spraying chamber, generally 6 meters is good.
⑸ Powder Spraying Section
The most critical part of this section is the technical problem of the powder spraying master. In order to create good quality, it is still worthwhile to spend money on a skilled master
I hope that the above information can enhance your understanding of glass bottle production. For more than 20 years, we have been committed to continuous process improvement and technological innovation to achieve targeted production efficiency, adapting to the changing market demand for glass bottles, producing in a complete range, expanding product coverage, improving product quality, and enhancing the competitiveness of enterprises. If you have any problems or queries, you can come to us and hope that our rich experiences can help you.
- Contract:Jenny
- E-mail: sales4@glass-bottle.com;JLglassbottle4@gmail.com
- WhatsApp/WeChat: 0086-155-6378-8572
Reliable Glass Jar & Containers Manufacturer | JL Glass Co.,Ltd
Producing the best glass container for drinking & cosmetics, making the world more healthy & pretty!